A machine that sharpens veneer knives used in lathes for cutting round logs. Sharpening is performed by two types of equipment. The Knife Grinder ARTESA I performs rough knife sharpening and is mainly used for base grinding. The Knife Honer ARTESA II performs precision honing of small knife angles along knife edges that have been ground by the Knife Grinder ARTESA I.
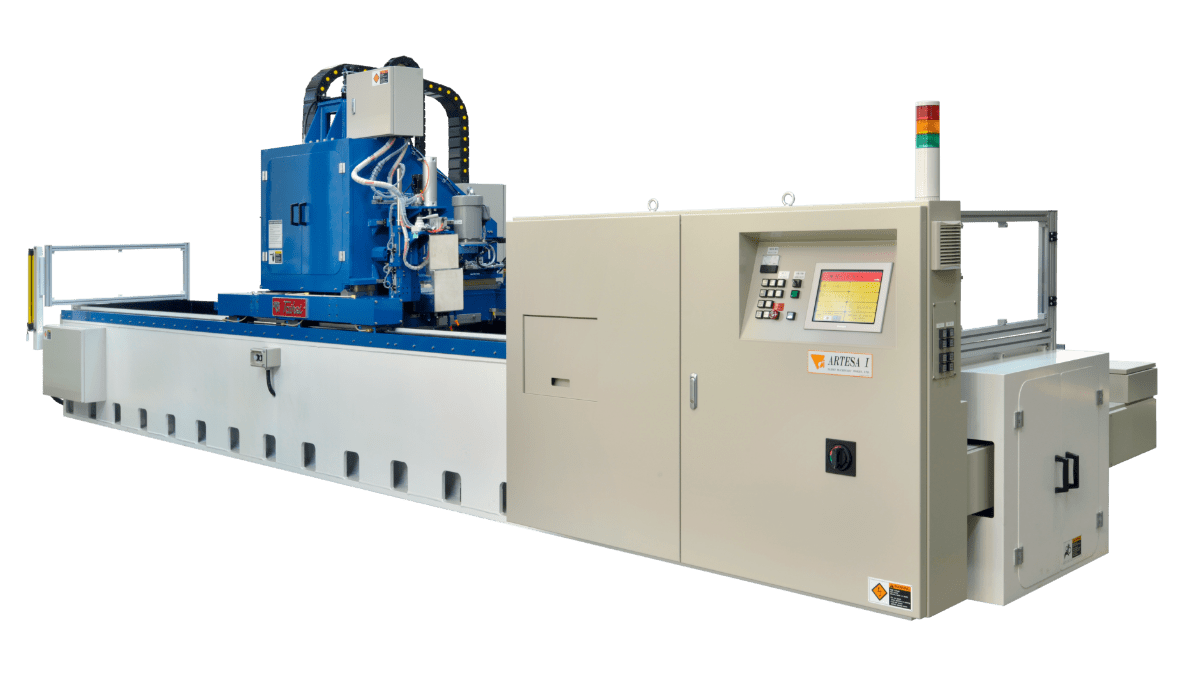
What properties does a knife need to produce high-quality veneer?
01STRAIGHTNESS
When peeling logs, the knife and nose bar must be straight and parallel.
Knife GrinderARTESA I V94-AC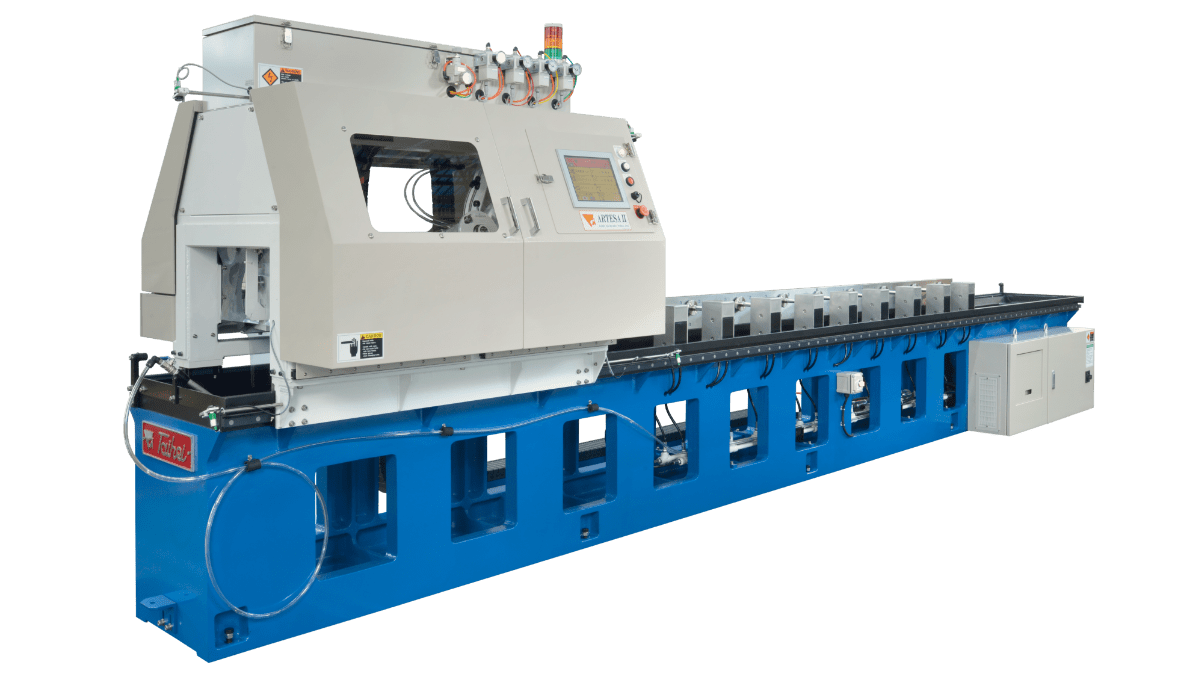
What properties does a knife need to produce high-quality veneer?
02SHARPNESS AND
EDGE RETENTION
Cutting edge chipping and bending is suppressed, improving veneer surface quality. Blade life and lathe uptimes are extended, helping to boost production volumes.
Knife HonerARTESA II V95-ACBenefits of installing both the Knife Grinder ARTESA I and Knife Honer ARTESA II
-
Improved veneer quality
The Knife Grinder ARTESA I sharpens knives with high straightness precision, while the Knife Honer ARTESA II makes it easy to reproduce the optimal blade shape for every application. This increases the accuracy of shaving parameters along the lathe and enables the production of consistently high-quality veneer.
Cost savings
-
Reduce raw timber costs by shaving low grade logs
When the Knife Grinder ARTESA I is used together with the Knife Honer ARTESA II, it becomes possible to hone knives even more precisely for even smoother veneer peeling. This makes it possible to shave even low-grade logs of poor quality, thereby reducing the log costs.
-
Reduce maintenance costs and maintain knife quality with highly precise and consistent sharpening
Grinds the knife blade into a parabolic shape, with a fine land width and obtuse cutting edge that maintains veneer surface quality over a long period of time. Leaves fewer hollows or chips knife edges, for a longer knife usage time and reduced maintenance costs.
-
Improved yields
High-precision knives produce a smooth veneer surface, which reduces the amount of sanding required during finishing. The resulting veneer is also stiffer and smoother, making it easier to handle and reducing the amount of glue required during processing. Also, this increases the number of obtainable face and back veneer, because veneers can be peeled thinner than usual. Lathe splitting during shaving is also reduced, which means less damage during stacking, reeling, unreeling, and drying. The number of joints in the composing process are also reduced, which increases production efficiency.