Horizontal Hot Press/
P25-AB
This machine handles the heat and pressure gluing process, the important final process in turning veneer into plywood. Unlike with conventional vertical presses, Taihei uses a method in which the heat plates are mounted vertically, and pressure is applied horizontally to the plywood.
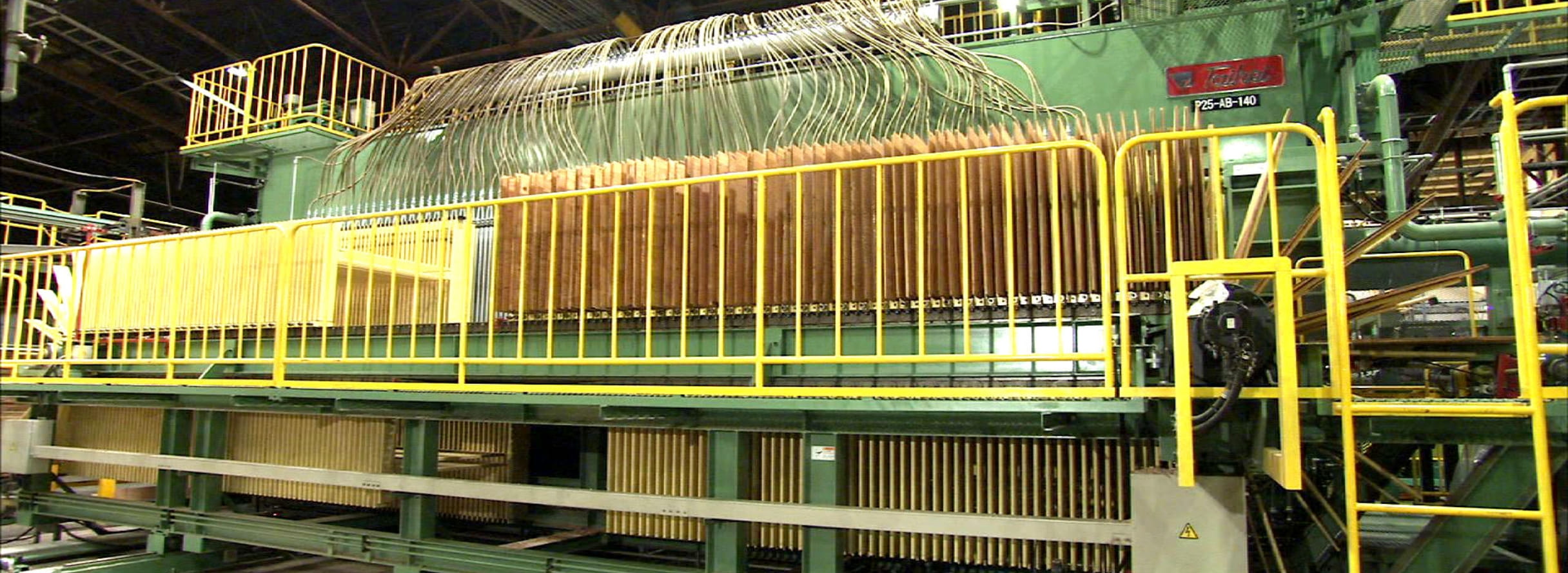
POINT
- Ideal uniform pressure enables the production of high-quality plywood
- Minimal thickness reduction increases production yield
- Up to 200 kinds of plywood can be produced with one-touch operation
- Handles many multiples of stacks, significantly increasing production per unit
- Does not need foundation pit, reducing foundation construction costs
- Heat plates are moved horizontally, which reduces energy costs
- Automatic infeed device (IRETARO) and automatic stacker provide fully automated operation
-
Reducing plywood thickness reduction
In a vertical press, the weight of the heat plates and plywood means contact pressures are different at the top and bottom of the pressed stack. However, in a horizontal press, the heat plates are mounted vertically, and this eliminates differences in contact pressure. This means that pressure can be applied evenly at lower pressures, avoiding non-uniform thickness in the final product and reducing thickness loss in the plywood.
-
No need for foundation pit/accumulation tanks
The machine is installed directly on the floor, eliminating the need to build a deep and costly foundation pit. Because the heat plates are vertically mounted, the overall height of the machine is reduced, meaning it can be installed in buildings with lower ceiling heights. Not only are foundation construction times and costs reduced, the time required for subsequent installation work is also reduced compared to vertical type machines. This makes it easy to upgrade from an existing hot press. In addition, the horizontal type does not require accumulator tanks, which can save on the costs of nitrogen.
-
Improved productivity and reduced labor costs
The press has up to 140 slots, meaning large volumes of plywood can be pressed at once. In vertical presses, the typical maximum is 50 slots. Replacing two vertical presses with one 100-slot horizontal press reduces the number of operators required. Under automatic mode, the machine requires only one operator, regardless of the number of slots used. Heat plates are 22.5 mm thick (40 mm in vertical presses).
Note: Numbers vary according to specifications. -
Operation and maintenance safety
The horizontal press stands lower than a vertical press, and the foundation pit can be made more shallow (or there is no pit at all, depending on the specification). This reduces the risk of falling, making maintenance work safer and easier and improving operator safety.
Options
Automatic Infeed Device “IRETARO”/P91-AB
Automatic separator with two-panel detection significantly reduces two-panel feeding.
Provides high-speed feeding of up to 100 thin panels, without damaging the panels.
Can handle a wide range of panel thicknesses, and is compatible with both horizontal and vertical presses. Optional pallet auto-return system available. (Improving the work process also makes pallet auto-detection possible.)
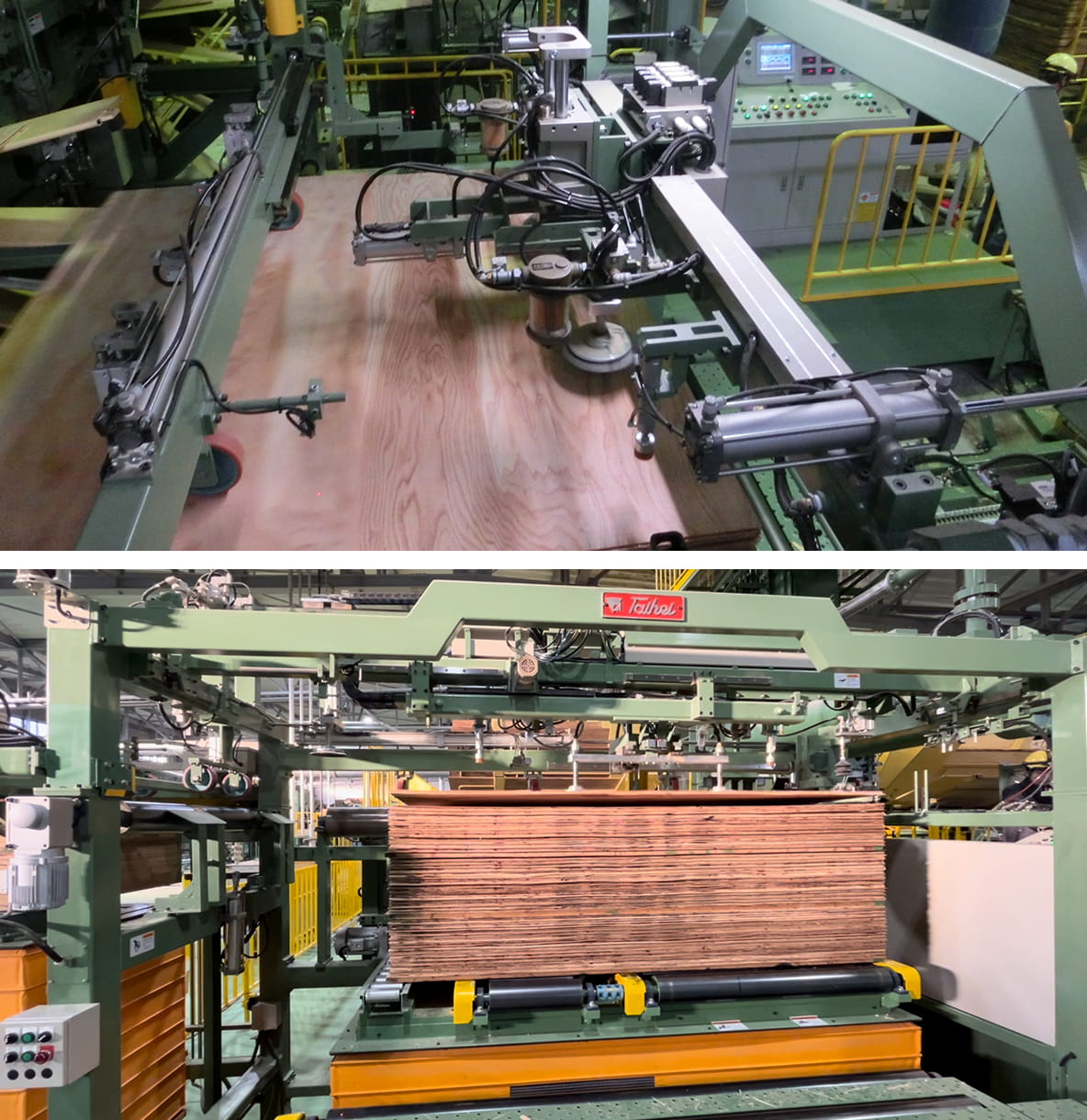
Standard Specifications
- Feeding system
- Suction method with vacuum pads
- No. of vacuum pads
- 2
- Pallet pinch rollers
- 1 set
- Thickness/weight detection
- 1 set
- Feed pinch roller device
- 1 set
- Pallet loading box
- 1 set